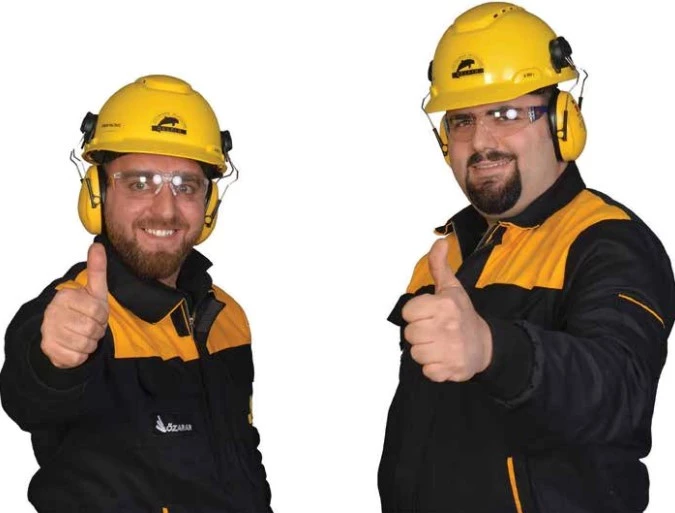
Toyotetsu Türkiye ve Delfin Vinç Servisi, binanın konstrüksiyonundan ayrı olarak yukarıya ve aşağıya doğru hareket edebilen 520 metrelik Yürüme Yolu projesini ortaklaşa çalışmayla hayata geçirdi. Projeyle birlikte 15 günlük bir çalışmayla giderilebilecek bölgesel hasarı, 1 saatte giderebilecek hale getirildi.
2001 yılında kurulan ve otomotiv yan sanayi sektöründe müşterilerine hizmet sunan Toyotetsu Türkiye ve Delfin Vinç Servisi son olarak binanın konstrüksiyonundan ayrı olarak yukarıya ve aşağıya doğru hareket edebilen 520 metrelik Yürüme Yolu projesini ortaklaşa çalışmayla hayata geçirdi. İlk kez Toyotetsu’nun Gebze’deki fabrikasında gerçekleştirilen ve 12 gün gibi kısa bir sürede tamamlanan projeyle, 15 günlük bir çalışmayla giderilebilecek bölgesel hasar 1 saatte giderebilecek hale geldi. Toyotetsu Makina Bakım Kıdemli Müdürü Ali Kahraman, “Burası yaşayan bir fabrika var, sürekli hareket ediyor. Aynı zamanda deprem bölgesindeyiz. Küçük depremler veya konstrüksiyonlarda değişiklikler olabiliyor. Bunun düzeltilmesi için uzun bir zamana ihtiyaç var. Biz söz konusu işi ortaklaşa çalışarak yaptık ve zamandan tasarruf ettik.” diyor. Toyotetsu Makina Bakım Kıdemli Müdürü Ali Kahraman ve
Delfin Vinç Servisi Genel Müdürü Mete Özarar ile bir araya gelerek uzun yıllara dayanan iş birliklerini, hayata geçirdikleri son dönem projelerini, gelecek dönem planlarını ve Endüstri 4.0’ı konuştuk.
Firmanızın yapılanmasından ve 2019 yılı iş gündeminizden bahsedebilir misiniz?
Ali Kahraman: Toyotetsu olarak, otomotiv yan sanayinde uzmanlaşmış bir firmayız. Şekerpınar’daki TOSB-Otomotiv Yan Sanayi İhtisas Organize Sanayi Bölgesi’nde konumlanan üç fabrikadan oluşuyoruz. İki fabrikamızda otomotiv parçaları üretiyoruz. Bir fabrikamızda da kalıp üretimi yapılıyor. Modeller,
kalıplar, dizaynlar yurt dışından geliyor. Biz burada kalıplarını yapıyoruz veya üretim hatlarını yönetiyoruz. Japonya’dan da bazen destek aldığımız oluyor. Bünyemizde Ar-Ge merkezimizde var. Mühendislik Birimi ve Enerji Yönetimi gibi toplam 10 birimden oluşuyoruz. Yaklaşık 90 kişilik bir ekibimiz bulunuyor. Biz bakım ekibi olarak, üç fabrikanın makina ve elektrik gibi sorunlarının giderilmesinden sorumluyuz. Gün içinde çıkan acil arızalar, planlı bakımlar, kestirici önleyici bakımlar gibi konularda sürekli destek veriyoruz. Kestirimci bakımı Endüstri 4.0’ın desteğiyle birlikte güçlendirme çalışmalarımız sürüyor. Şu an bir makinamızda pilot uygulama yaptık ve halihazırda ondan veri topluyoruz. Söz konusu verileri derledikten sonrada diğer makinalarımızda da yaygınlaştırmaya devam edeceğiz.
Ar-Ge merkezinizde ne gibi çalışmalar yürütüyorsunuz?
Ali Kahraman: Ar-Ge merkezimiz bünyesinde kolaboratif robotlar, özel yazılımlar, kaynak mühendisliği, pres mühendisliği, tasarım ve proje gibi Toyotetsu Makina Bakım Kıdemli Müdürü Ali Kahraman çalışmalar yürütülüyor. Bizde bakım ekibi olarak onlarla iş birliği içerisinde çalışıyoruz. Bizim projelerimiz, fikirlerimiz oluyor. Özellikle Endüstri 4.0’la ilgili makinaları akıllı makina haline getirme, eski teknolojimizi son teknolojiye dönüştürme konusunda çalışmalar yapıyoruz. Bu kapsamda üniversitelerden, otomasyon firmalarından destek alıyoruz. Mesela ilk patent çalışmamız bana ait. Çoklu somun dağıtıcı bir ünite yaptık. İşletmemizde kullandığımız somun besleme makinalarını 4-5 hatta yaygınlaştırarak tek bir noktadan kullanabiliyoruz. Hem eğitim hem de iş güvenliği alanında kullanacağımız VR (Sanal Gerçeklik) çalışmamız var, bunu geliştirmeye devam ediyoruz. Örneğin ben uzaktan VR gözlükle ekip arkadaşıma ya da makinaya destek vereceğim. Üniversitelerle ortak çalışmalarımız, sosyal sorumluluk projelerimiz oluyor. Son olarak öğrencilerle ve ekibimizden çalışanlarla beraber Kartal sahilde kıyı temizleme çalışması yaptık.
Üretim parkurunuzda ne tür tezgahlar ve robotlar var? Hangi markalarla çalışıyorsunuz?
Kaynak fabrikamızda genelde Yaskawa marka ro- botlar kullanıyoruz. Servis konusunda iyi ve kaliteli hizmet veriyorlar. Herhangi bir problemle karşılaştı- ğımızda bize anında destek oluyorlar. Spot kaynağı, gaz altı kaynak robotları ve taşıma ro- botlarımız var. Çeşitli proseslerde yaklaşık 150 adet robotumuz çalışıyor. Pres hatlarımızda ise transfer preslerimiz, blanking preslerimiz var. Bunların haricinde sıcak pres hattımız ve lazer kesme proses- lerimiz bulunuyor.
Delfin Vinç ile iş birliğiniz kaç yıldır devam ediyor? Birlikte ne gibi projeler hayata geçirdiniz?
Ali Kahraman: Biz Delfin Vinç ile fabrikamızın kuruluşundan beri, yaklaşık 18 yıldır birlikte çalışıyoruz. Ancak onlardan sadece imalatçı veya servis tarafında destek almıyoruz. Aynı zamanda Kaizen, Yalın Üretim ve Endüstri 4.0 gibi konularda da destek alıyoruz. Kalıp kaçırma, iş kazalarını minimize etme gibi konularda da ortaklaşa fikir alışverişinde bulunuyoruz. Mesela başarılı bir çalışma yaptılar. Kalıbın kontrolsüz bir şekilde aşağıya doğru kaymasını engelleyecek bir yapı oluşturdular. Sistem sorunsuz, düzenli bir biçimde çalışıyor. Özel bir program yazdılar, en ufak bir sallantı bile olsa sistem devreye giriyor ve uyarı veriyor. Hem mekanik anlamda hem yazılım anlamında vinç üzerinde iki türlü önlemleri var. Eğer mekanik anlamda büyük yatırıma giremiyorsanız, diğer ekipmanlar ve yazılım anlamında işi çözebiliyorsunuz. Çünkü yapı değişeceği için de büyük maliyetler oluşuyor, bu sefer daha kompakt bir çalışmayla işi çözme yoluna gidiyorsunuz.
Mete Özarar: Tabii şimdi işin içinde bir denge var. Önlem alırken ekonomik durumları da göz önünde
bulundurmak gerekiyor. Sürekli yatırım yapmak değil de var olanı modernize etmek, günümüz şartlarına uyarlamak da tercih ediliyor. Yeni bir vinç yatırımı yapılmayacaksa, olanı iyileştirmek, yeni çıkan ürünleri vince adapte etmek, yeni bir güvenlik sistemi çıktığında bunlara uyarlamak veya güncel- lemek hem maddi hem de manevi açıdan çok daha makul ve mantıklı oluyor.
Son dönemde birlikte gerçekleştirdiğiniz projenizden bahsedebilir misiniz? Mete Özarar: Geçen yıl 520 metrelik bir Yürüme Yolu projesinde ortaklaşa çalıştık. Burada yeni bir sistem denedik. Yürüyüş yolunun tamamen binanın pozisyonundan ayrı olarak, yukarı ve aşağıya doğru hareket edebilir şekilde bir sistem geliştirdik. Bu zaman içinde orta ve uzun vadede binanın içindeki oturmalarda, normal şartta 15 günlük bir çalışmayla giderilebilecek bölgesel hasarı 1 saatte giderebiliyoruz. Bu çok büyük bir yenilik ve ilk kez bu fabrikada yapıldı. Normalde 1,5-2 ay sürebilecek projeyi iş birliği içerisinde, Toyotetsu ile ortaklaşa çalışmayla yaklaşık 12 günde tamamladık.
Ali Kahraman: Mesela binamızda veya planımız- da harekette bir değişiklik olduğu takdirde, Delfin Vinç sahaya gelip en fazla 1 saat içerisinde sorunu çözecek. Ölçümünü alacak, programından bakacak sorunun olduğu yeri tespit edecek ve ayarını yaparak işlemi tamamlayacak. Geçmişte kaynakların kesilmesi, hesaplanması, raylar oturtuluyor, tekrar kaynaklar patlatılıyor yapılıyor vb. Bunu şimdi bir vidayla, bir anahtarla açıyor yapıyorsunuz. Şimdi sadece 10 dakikalık bir ayarla bütün fabrikanın yürüme yolunu kaldırıp indirebiliyorsunuz.
Projenin geri dönüşlerinden bahsedebilir misiniz? Size ne gibi kazanımlar sağladı ya da sağlayacak?
Ali Kahraman: Burası yaşayan bir fabrika var, sürekli hareket ediyor. Neticede deprem bölgesindeyiz. Küçük depremler veya konstrüksiyonlarda değişiklikler olabiliyor. Bunun düzeltilmesi için uzun bir zamana ihtiyaç var. Biz söz konusu işi 15 günde yaptık. Ama şimdi bunu bir pazar günü 2 saat içerisinde çözebileceğimiz bir yapıya dönüştürmüş olduk.
Mete Özarar: En önemlisi de olası bir İstanbul depreminde böyle bir felaket olduğu takdirde, fabrikada bir kısımda çökme yaşandığı zaman bir gün sonra bu fabrika tekrar üretime geçebilecek, çalışabilir hale gelecek. Normal şartlarda bir fabrikada hatların düzelmesini 1 ay beklemesi gerekiyor.
Delfin Vinç ile çalışmayı neden tercih ettiniz?
Ali Kahraman: Fabrikamızın kuruluş esnasında Japon Yönetimimiz Özarar Vinç ile çalışmayı tercih etmişti. Biz de Özarar ile birlikte Delfin Vinç ile çalışmaya başladık. Öncelikle servis açısından bir memnuniyetimiz var. Ayrıca lokasyon açısından fabrikamıza yakın olmaları önemli bir etken. Örneğin herhangi bir problemde 15 dakikada gelip müdahale edebiliyorlar. Geçmişten gelen bir çalışma sürekliliğimiz bulunuyor. Bu da bizim için büyük bir avantaj oldu. Japon menşeli bir firma olmamız nedeniyle iş sağlığı ve güvenliği, çalışma kuralları gibi özellikle dikkat edilen hassas noktalarda çalışma sistemimi- ze en iyi uyum sağlayan firma olması açısından da önemli. Ayrıca deneyimli, işini bilen ve esnek bir ekibe sahip oldukları için hem iş takibimiz kolaylaşıyor hem de bir sorun karşısında anında çözüm üre- tebildikleri için bizim de işimizi kolaylaştırıyorlar.
Sizin açınızdan çalışma süreci nasıl geçti?
Mete Özarar: Bizim açımızdan keyifli ama zorlayıcı bir süreçti. Planımızı, programımızı yaptık, inanarak başladık ve sorunsuz bir şekilde tamamladık. Japon firması olduğu için iş güvenliğinde daha fazla noktalara dikkat ediliyor, oldukça hassaslar. Biz bunların hepsini karşılıyoruz. Vinç firmaları arasında ilk olarak aldığımız OHSAS İş Güvenliği belgemiz var. Tüm kurallarını harfiyen uyguluyoruz. Burada önemli bir nokta da iş yaparken hem maksi- mum güvenlik tedbirlerini alıyoruz hem de olası iş kazalarına karşı müşterimizi sigortayla da güvence altına alıyoruz.
Önümüzdeki dönemde ortaklaşa devreye almayı planladığınız proje/projeler var mıdır?
Ali Kahraman: Evet, var. Birlikte vinçlerimizin çalışma sınıflarını yükselteceğiz.
Mete Özarar: Vinç modernizasyonları yapacağız. Halihazırda 20 senedir çalışan vinçler var, bunların günümüz teknolojisine uyarlanması, sınıflarının yükseltilmesi, ekstra güvenlik sistemlerinin uygulanması ve Endüstri 4.0’a geçiş için altyapısının hazır olarak üretilmesi gibi çalışmalarımız var.
Genel merkezinizden iyileştirmeye yönelik talepler geliyor mu?
Ali Kahraman: Kendi içimizde çok iyi bir iletişim ağımız var. Japonya’da ya da globalde bir fabrikada iyileştirme yapıldığı zaman diğer yerlere de “siz de bunu yapın” diye uyarılar geliyor. Mesela Türkiye’de vinçin altındaki pendantın taşıma yeri boydan boyadır. Japonya’da bir uygulama gördük. Mete Bey, “Bu uygulama bizim hoşumuza gitti. Türkiye’de daha önce hiç yapılmamış, Avrupa firmalarında da görmedim” dedi. Şimdi vinçlerimizin modernizas- yonlarıyla birlikte onu da yapacaklar. O da güzel bir çalışma olacak.
Mete Özarar: Evet, çok önemli bir proje. Japonya’da yapılmış, ilk denemesi burada yapılacak.
Endüstri 4.0 konusundaki çalışmalarınızla ilgili bilgi verebilir misiniz?
Ali Kahraman: Endüstri 4.0’a geçişin başladığını söyleyebilirim. Yakında Endüstri 4.0’ın meyvelerini toplamaya başlayacağız. Özellikle maliyetlerimizi azaltma noktasında önemli avantajlar sağlayacak. Bir makina bozulduğu zaman hem duruştan kaynaklı maliyetler hem de makinaya verilen zararlar mad- di anlamda büyük bir külfet oluşturuyordu. Endüstri 4.0’la birlikte bunları minimize etmeyi planlıyoruz. Fabrikadaki çalışma şartlarına göre Endüstri 4.0’da olanaklar sonsuz. Sürekli verileri toplayalım, tüm veriler aksın, geriye dönük arıza tespiti yapabilelim istiyoruz. Örneğin tork motorun bir zorlanma olduğunda, motor gru- bundaki bir balata diskinin, balata aşındığında vb. durumlarda bize alarm versin istiyoruz. Periyodik bakımlarını hem kendileri hem de biz gerçekleştiriyoruz ama 24 saat kontrol altında tutmak adına çalışmalar yapıyoruz.
Mete Özarar: Endüstri 4.0’ın en büyük katkısı, servis sürelerinin optimizasyonu konusunda oldu. Endüstri 4.0’a tamamen geçildiği zaman servis süreleri optimizasyonunda çok faydası olacak. Maliyetleri kontrol altına alabileceğiz, veriye dayalı değişimler yapılacak, saatlik bakımlara geçilecek. Şu anda 3 ayda bir bakım gerçekleştiriliyor ancak makinanın kullanım sıklığı doğrultusunda bu rakam değişiklik gösterebiliyor.
Endüstri 4.0’la ilgili Toyotetsu’dan size talepler geliyor mu?
Mete Özarar: Evet, talepler geliyor.
Ali Kahraman: Aslında biz zorluyoruz. Hemen hemen her hafta toplantı yapıyoruz. Kalıbın güvenli apliği çalışma alanı var. O çizginin alanına taşıma esnasında kimsenin girmemesi lazım. Mete Bey’den çalışmayı talep ettik, deneme yaptık. Şimdi biraz daha düzeltmesini, iyileştirme yapmasını istedik. Tamamlandığı takdirde, çalışma Türkiye’de bir numara olacak. Daha önce hiçbir yerde yapılmadı. Açıkçası biz süreci kolaylaştırmak istiyoruz. Makinalarımıza Endüstri 4.0’la ilgili bir sürü ekipmanlar takıyoruz. Makinalarımıza gün içerisinde bir sürü arıza kodu geliyor. Mete Beylerin ekipmanlarına da bağlayacağız, yüzlerce arıza gelecek. Söz konusu arızalardan gerçek arızaları belirlemeleri için anomaly detection (anomali tespiti) yapmalarını isteyeceğiz. Bu konuda Mete Bey’in tecrübesinden yararlanacağız. Biz sistemin, yapay zekanın gerçek hatayı tespit etmesini bekliyoruz. Şu aşamada zor ancak vinci, pres makinasını, robotu iyi bilen uzmanlar o korelasyonu kuracaklar ve bize destek olacaklar.
Mete Özarar: Vinçler üretilirken normlara göre üretiliyor. Ama şimdi sensör koyup, tekerleği ya da redüktör çıkışının, milinin ısısından hata aradığınız zaman bunun bir standardı yok, denemeyle yapmanız lazım.